摘要:本文主要对目前汽车行业供应商在产品量产阶段存在的主要质量问题进行归纳说明,并对如何进行此类问题分析整改提出相应对策,确保供应商质量得到有效提升。
关键词:供应商;质量;提升;
在汽车行业,主机厂均在培养核心供应商,以便与其建立“利益共同体”,确保主机厂、供应商均得到可持续发展。而供应商在量产后的质量表现是主机厂衡量供应商优劣的主要指标,因为量产供应商的质量直接影响到整车产品质量,继而影响到市场口碑、销量等,从而如何有效提升供应商质量,使其成为主机厂核心供应商,成为目前主机厂质量工作的关键课题。本文主要对如何做好供应商量产后的质量提升工作进行分析说明。切忌在提升过程中以供应商处罚为导向,处罚仅作为辅助工具,督促供应商提升的辅助手段。
1量产阶段供应商主要问题
如需开展供应商质量提升,首先需明确供应商存在哪些问题。量产阶段供应商质量问题从问题来源主要分为两大类:研发阶段遗留问题与量产阶段新增问题。
1.1研发阶段遗留问题
研发阶段遗留问题从产生角度主要来源于以下几方面:
(1)验证周期不足导致问题未有效识别,主要由于验证时间或里程等不足导致。比如:抗腐蚀零部件盐雾试验时间不足,导致使用时间较久后,出现腐蚀。整车行驶较长里程后,出现零部件装配松动问题,产生异响异振等问题;
(2)验证工况识别不充分导致。比如:在温度极低环境出现机油乳化,空气稀薄环境出现车辆启动困难等;
(3)驾驶员车辆使用极端情况未有效识别。比如:长期怠速出现车辆抖动,连续启动出现车辆启动困难等;
(4)风险识别不充分导致问题未有效关闭。比如:研发阶段已识别该问题,但风险预估错误,认为发生概率较低,导致在市场发生批量问题;
(5)小批量试装验证不足导致问题流入量产。比如小批量试生产未按照最高节拍生产,导致量产后按照最高节拍生产出现人员操作时间不够出现错漏装、设备满负荷长时间运转出现故障等。
1.2量产阶段新增问题
量产阶段新增问题从产生角度主要来源于生产过程管理不当导致,即4M1E变更管理不善导致,生产过程出现波动导致。换个角度进行说明,按照产品开发流程中的里程碑节点进行说明:
(1)OTS认可节点:如果产品正常通过OTS工装样件认可,至少可以说明产品两大关键任务顺利完成。
①产品正常通过OTS认可,说明通过试验,产品满足设计者的技术要求;
②产品正常通过OTS认可,说明按照目前工装及工装参数进行生产,可以生产出满足设计者技术要求的产品。
(2)SOP认可节点:如果产品正常通过SOP认可,则可以说明,按照目前的生产过程,可以批量生产出满足设计者技术要求的产品。该生产过程包含:物流包装、原材料、工装设备一致性、工艺流程、作业手法、节拍、人员(包含操作员工、管理员工)等,所有过程均包含在内。
理想状态:SOP认可后,整个生产过程完全稳定,没有任何变化点。包括但不限于:人员没有任何变化,比如离职、请假、情绪波动、并且完全按照作业指导书操作等;工装、设备、器具等没有任何变化,比如磨损、故障等;材料没有任何变化,比如成分变化、性能变化等;相关标准、工艺文件等没有任何变化且操作性良好,比如生产节拍不变等;整个生产环境没有任何变化,如温湿度均衡等。在此生产过程完全稳定的理想状态下生产,产品一致性极佳,存在由于工装设备的公差导致产品存在些许差异,但均满足技术要求,在此理论状态下产品100%合格。
但在实际生产过程中,存在各种变化,导致生产过程不稳定,从而导致产品质量一致性出现波动,继而导致不合格品的出现。举例如表1:
表1各类变化点可能导致问题
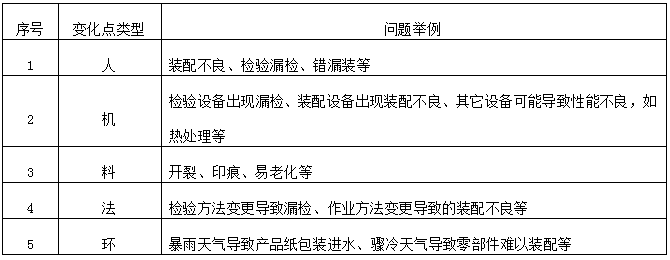
2质量提升思路
前面部分对量产供应商主要存在哪些问题进行了分类说明,下述将对如何进行量产供应商质量进行提升进行说明。解决的前提是首先对问题进行分类:研发阶段遗留问题或者量产阶段新增问题。
2.1研发阶段遗留问题解决思路
解决研发阶段遗留五类问题前四类,直接反馈设计者,对技术要求进行修订重新定义产品,等同于做一次设计变更,流程与重新开发一次产品相同,以问题为导向,解决相对比较直接。研发阶段遗留问题整改思路举例如下:
(1)产品材料性能不满足要求:重新选择材料,定义材料性能;
(2)产品外观结构不合理:修改或者重新开发工装,比如现阶段产品结构不合理,需要重新开发模具;
(3)产品软件性能不满足要求:目前汽车产品智能化、网络化发展,软件功能愈发强大,随之而来软件问题增加,涉及软件类的可能需要重新进行软件升级;
设计变更的一个最大特点是对图纸、数模、技术要求等于产品设计定义相关的技术文件进行修改。但设计变更随之而来的会对过程产生影响,从而产生过程变更,所以企业在设计变更判定中,需明确是否对过程有影响,尤其是涉及法规类。举例如下:
(1)生产/检验作业指导书是否需要变更;
(2)油液加注量是否需要变更;
(3)打胶量、打胶轨迹是否需要变更;
(4)焊点数量、位置是否需要变更等。
对于研发遗留第五类问题,需要以过程为导向,因为问题产生根本原因为生产过程发生变化导致,如上述举例节拍发生变化,导致人员、设备等不能满足需求,从而产生质量问题。对于此类问题解决,主要通过IE分析,提升稼动率来保证,举例思路如下:
(1)导入新工装设备:使物流提速、装配便捷快速等确保生产效率更高,满足节拍需求。此类解决方法相对投入较大,较多主机厂在春节或者销量淡季进行产线布局整改、工装设备变更等相关工作;
(2)工艺改进:将现有生产工序重新拆分、合并、排序。取消多余工序,如步行取件工序,由1人取件时顺便将下工序用件领取等;合并工序,如将螺栓打紧由第一道工序预紧,第二道工序打紧,合并为一道工序完成预紧、打紧工作。或者比如条形码扫描工作较多且分散,合并集中后重新分布在几个工位完成;拆分工序,如将管路一道工序安装完成,改为第一道工序预装,第二道工序打紧完成。此类解决方法需要对工艺有完善的掌握,确保去除的工艺不影响质量。
2.2量产阶段新增问题解决思路
前面已经说明,量产阶段的问题主要由于过程管理不善导致。所以对于此类问题的解决需要以过程为导向,将整个生产过程进行排查,找出所有对质量有影响的风险点,对症下药,最终形成一套完整过程监控及运行机制。举例如下:
2.2.1人员管控思路
4M变更管控中,最难管控的即人员,所以4M中将人排在首位,因为预知性比较差。对于人员如何管控,首先要清楚人员可能存在的变化点,举例如下表2:
表2人员变化点类型及对策
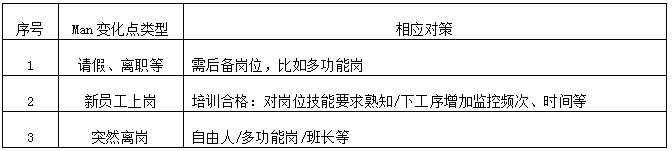
2.2.2工装设备管控思路
4M变更管控中,第二管控模块为工装设备。工装设备的管控第一难点在于,前期工装设备的MSA分析,目前较多供应商对于MSA分析基本属于敷衍主机厂,而主机厂供应商管理人员由于专业能力较弱,所以MSA分析的有效性基本不能有效识别。导致MSA分析基本属于失控状态。其实MSA分析主要关注于:精度、准确、一致性即可,由于MSA是质量五大工具之一,需要专门培训讲解,所以在此不做具体介绍。如MSA有效,则量产后工装设备的管理关键点在于维保点检,维保点检要求的制定专业性较强,必须对工装设备非常了解。从上述说明可以看出工装设备的管控思路与人员管控略有不同,工装设备的变化可预知性比较强,有规律可循,而人员预知性比较差。所以工装设备管控举例如下表3:
表3工装设备变化点预防管控思路
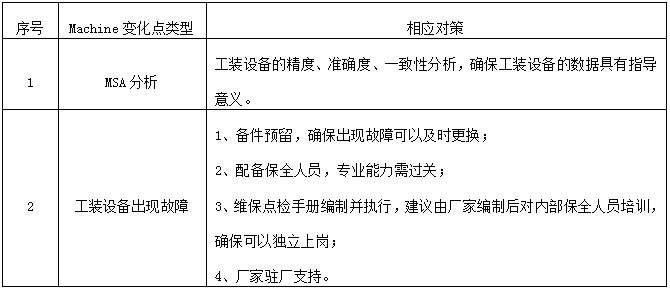
2.2.3材料管控思路
4M变更管控中,材料变化导致出现的问题较少,因为在工装样件认可中,材料已经属于各主机厂重点关注对象,甚至开始指定材料类型、厂家等,所以材料管控在此不做过多说明。只需要做好以下几点工作即可:
(1)材料类型需要确定;
(2)由于材料与环境等相关性较大,比如温度稍高,性能即可能受影响,所以必须做好每批材料的抽检工作,并要求保存检测结果,便于追溯。
2.2.4法管控思路
4M变更管控中,法的范围较多,各类技术工艺文件均属于法的范畴,任何变更基本都会引起文件的变更,所以变更频次较多,但管控相对比较容易。需要有相关文件支撑管理,比如变更管理文件。所有变更均需明确一点:是否需要文件变更,比如工序流程图、作业指导书、检查成绩书等。具体在此不做举例介绍。
2.3整体监控思路
上述是按照模块介绍如何提升供应商质量,下面将各模块梳理形成体系化的提升思路进行说明。
2.3.1问题梳理
提升第一步:对供应商进行审核。明确供应商现有问题,最直接的方法是开展体系审核、过程审核、产品审核、问题审核。
2.3.1.1体系审核
明确目前供应商质量管理体系的有效性,最直接的判定方法是:
(1)是否具有合格的体系员;
(2)公司是否给予充分的授权;
(3)公司是否有并按照计划开展相关审核。
按照上述对供应商进行确认并要求执行。
2.3.1.2过程审核
明确目前供应商生产过程的适用性。此审核已过程为导向,明确供应商生产过程是否存在导致质量不合格的风险。最直接的判定方法是:
(1)如有体系员,并按计划开展对应过程审核,确认其审核结果及问题跟进结果;
(2)上述如未开展,则需要主机厂对其进行过程审核,并明确其过程现有问题点,同时跟进供应商整改;
(3)确认现有工艺文件是否具有保证质量的能力,此过程专业要求较高,需结合产品开展;
(4)审核的最简单方法是确认目前生产过程是否按照现有工艺文件执行;
(5)结合第三点与第四点对其文件及文件执行情况进行修订整改。
2.3.1.3产品审核
明确目前供应商生产过程中的半成品、成品是否满足质量要求。最直接判定方法是:
(1)供应商在主机厂的质量表现,即其成品是否满足质量要求;
(2)供应商生产过程中的检测记录即可说明其半成品是否满足质量要求。前提是供应商有真实的开展过程检验;
(3)抽取过程中半成品、成品进行检验。抽样一定要能代表生产过程。
2.3.1.4问题审核
以供应商目前的质量问题为依据,开展审核,明确产生的问题的根本原因,从而推动供应商整改提升。
2.3.2问题整改
问题梳理完成,则按照对应问题制定对策进行提升。在开展提升的同时,供应商及主机厂的遏制检验需同步开展,杜绝不合格品的流出与流入。
3案例介绍
下述以某主机厂焊装供应商举例进行说明提升步骤。前期该供应商在主机厂质量问题较多:主要表现为零部件清洁度差导致焊装出现多次无法焊接,零部件精度差导致总装装配困难等,甚至零部件强度不达标等。
步骤1:主机厂形成专项提升小组,成员包含主机厂SQE、主机厂焊装品质人员、供应商品质人员、供应商生产人员等;
步骤2:梳理供应商现阶段在主机厂的所有问题,形成问题清单,并要求供应商开展遏制检验,同时派驻主机厂检验人员进行驻厂遏制检验,杜绝不合格品的流出与流入;
步骤3:将所有问题落实在生产过程当中,将风险过程全部进行整改。主要对工装设备有效性进行确认:即对工装设备进行MSA分析,确认其精度、准确度、一致性。根据分析结果对工装设备进行调整;
步骤4:在工装设备稳定的基础上,以主机厂焊装过程管控方案为模板梳理过程要素,以此过程要素对供应商开展相关审核,并且将4M变更管控作为重点对其提出相应要求,如体系员要求、审核频次等。并且以问题为基础,对供应商进行培训。最终形成过程监控机制管控要素表,要求供应商按要素表执行,主机厂定期监控执行情况。确保供应商过程的稳定。如下表4。
表4过程监控要素表
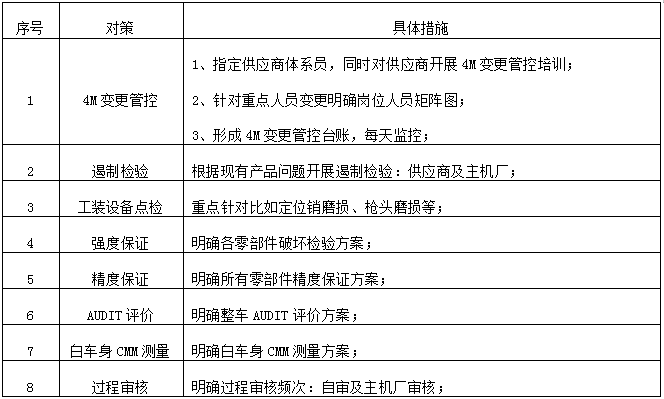
备注:所有措施需明确责任人、频次、输出物要求,关键进行问题跟进。
4结语
不同供应商在提升细节方面关注点肯定不同,主要原因还是供应商生产过程工艺不同导致。比如钣金焊接供应商重点需确认其冲压过程及拼焊过程的有效性,细述则比如定位销磨损、模夹检精度是否满足图纸要求、焊接枪头是否及时更换等等;线束供应商重点需关注前工序端子压接、导线与端子装配、后工序线束包扎等。但本文是将供应商提升是从体系角度进行说明,所有供应商提升均可套用该方法。
参考文献
[1]张成海著:《供应链管理技术与方法》,北京:清华大学出版社,2001。
[2]约翰·盖特纳(John L.Gattorna)著《战略供应链联盟:供应链管理中的最佳实践》,宋华等译,北京:经济管理出版社, 2003。