摘要: 针对当前飞机制造企业信息系统众多、质量信息数据来源不一致、对贯穿飞机研制全生命周期的产品设计制造过程数据及企业资源数据缺乏相应的数据治理与数据质量控制等问题,通过分析公司质量管理现状,构建基于大数据的质量管控体系,挖掘关键质量信息,建立QBOM目录结构的单机质量档案,实现产品质量管控模式从事后被动检验转变为事前主动预防,从而提高产品质量及成品率。
关键词:大数据、质量管控、QBOM、异地协同RFV、数据挖掘
1 引言
飞机制造是一个复杂的过程,质量可追溯性要求高[1]。目前成飞集团的质量管理处于质量统计阶段,百分之百全检的检验方式有效地保证了产品的质量及可靠性,然而对质量问题进行诊断、报警与维护的功能并没有充分发挥,如何更加迅速且准确的进行质量控制及预测成为了成飞目前在质量方面亟待解决的问题。作为一个航空类企业,成飞最大的生产特点就是多品种小批量。基于多品种小批量的生产方式,传统的质量控制方法在生产过程中出现了种种的不适应性,时常出现虚报及漏报的情况,造成生产过程无谓的停工检查及返工,从而大大提高了质量成本。
随着数字化与信息化建设的推进,公司各个生产经营系统积累了丰富的原始数据,为进行大数据分析奠定了基础。如何从这些数据中分析挖掘出关键质量信息,用于提高产品质量及成品率,是质量控制的重点方向。
进行基于大数据的飞机质量管控关键技术研究与应用是成飞的企业信息化发展到信息综合利用阶段的必然需求。
2 飞机制造质量形成过程分析
按照过程管理的模式进行划分,飞机制造质量的形成过程包括工艺指令下达、生产指令下达、物料配套、现场执行、质量记录五个阶段,最终形成单机质量档案,如图1所示。
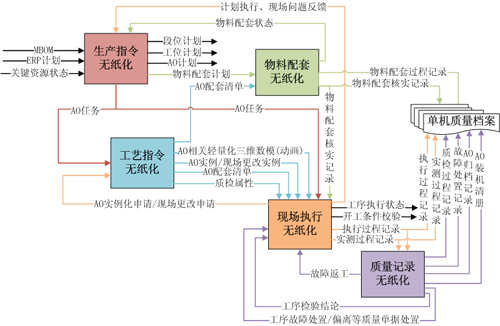
图1 飞机制造技术架构-质量数据集成
在工艺指令下达阶段,装配指令(ASSEMBLY ORDER,即AO)作为装配生产的制造依据,是非常关键的工艺技术文件,以AO无纸化为突破点来实现工艺技术文件的无纸化,重点突破AO实例化及基于实例的工艺现场更改无纸化技术难点[2],AO的实例化依据MBOM结构及AO文档的技术状态、有效性和版本管理来实现,为每个架次的AO生成一个独立的实例,物流配套信息、执行过程信息、质量数据的采集都以独立的AO实例为对象进行记录,为建立全数字化的单机质量档案提供数据支撑。三维轻量化数模及装配仿真动画作为装配制造的重要部分,将在AO实例化时一并实例化,在制造执行现场呈现给执行工人进行交互使用,以可视化方式指导工人进行装配操作。AO实例的现场更改则是基于独立的AO实例进行的工艺设计更改,其作用范围限定于AO实例的独立架次有效性范围内。AO在执行过程中,在更改流程驱动下可进行多次现场更改,每次更改将实时反馈到MES系统中,现场以最新版AO实例执行,确保现场使用的AO有效性。
在生产指令下达阶段,要解决生产指令生成、发布和传递无纸化。AO计划下达时将实时关联ERP库房管理模块的AO物料配套保障情况决定是否达到下达状态,同时关联PDM判定AO文档是否发布并具备架次有效性。满足物料配套条件和AO发布有效的AO计划才能下达,并成为工段的作业计划。工段将作业计划分派给操作者或操作小组,工人接收作业任务进行现场执行。通过计划的逐层分解及与物料配套、AO有效性的关联达到对生产的有效管控。
物料配套阶段保障装配生产计划顺利执行的关键,物料按计划节点及时配套才能保障生产的顺利执行。物料配套无纸化,从MES系统由AO的物料配套计划驱动,通过ERP库房管理模块进行物料配套、物料配送,在生产现场由MES系统进行现场物料接收、现场物料核实。在现场物料接收和核实环节,由工人、检验分别在无纸化AO文档上记录和核实物料的关键质量信息,包括物料图号、配套架次、质量编号、数量等。AO的配套物料信息和核实质量信息将作为AO开工条件检查的条件之一进行校验。在物料配交接环节使用二维码技术,进一步校对实物和信息流的一致性,确保物料实际配套的准确性。
装配现场执行阶段依据无纸化生产指令、无纸化工艺技术文件、无纸化物料配套信息。现场执行面向操作层的操作者、检验员。现场执行的无纸化包括:(1)AO实例化,由MES向CAPP提出AO实例化申请并获取AO实例;(2)工序开工条件核实,系统将自动进行工序开工条件检查,具备开工条件的AO允许进行工序的执行。(3) 工序的开完工信息采集,工人依据无纸化的工序说明书进行装配操作,并采集工序的开工、完工信息,涉及实测记录的工序填写相应记录。(4)现场可视化展示,装配现场执行无纸化以装配现场可视化为基础,在装配现场展示AO级、工序级的三维轻量化数模以及基于三维轻量化数模的装配仿真,指导工人操作,是现场工艺指导的重要辅助手段。(5)AO无纸化现场更改,通过对单架次应用的有效的AO实例更改,由一系列流程控制保障工艺现场更改的严谨性和现场执行的可行性。(6)工序质检及故障处置,对工序的质检及故障处置进行管控,按照质量程序文件要求自动进行工序开工约束控制,避免跨越工艺流程操作问题。(7)现场问题管理,处理现场执行过程中的问题,通过流程协同职能部门处理(8) 计划执行反馈,工序执行完成,将完工信息自下而上反馈至AO层、工位层、段位层,形成执行计划的管理闭环。在现场执行过程中通过流程驱动和技术手段,提高生产管控的自动化和敏捷性。
质量记录阶段飞机装配制对质量控制的规范性、完整性,准确性、可追溯性都有极为严格的要求,因此,在无纸化装配制造中,AO质量文件的无纸化归档尤为重要。AO归档的质量记录包括:(1)AO装配清册,记录飞机装配的物料信息、质量信息、核实信息,在从物料的配送到完工核实的流程中记录(2)设检工序的检验信息,记录工序检验的结论,由现场工序检验时记录完成。(3)现场实测记录表,记录制造过程中需实时测量的技术指标数据,由工人、检验等人员录入、签字记录完成。(4)工序故障及质量单据信息,由工序检验发起相关不合格品通知单、不合格品审理单等质量单据审理信息及处置结论(5)AO更改记录,记录AO的历史更改记录及现场更改的内容、签审信息等。(6)AO归档信息,由系统自动进行AO归档条件的综合判定,当AO执行完成并满足归档条件时,允许进行AO电子归档。AO的质量归档文件与质量证明文件、质量报告等其他质量信息一并汇总,以BOM为牵引形成单机质量档案。
3 基于大数据的质量管控
以全面提升成飞公司飞机制造质量管控水平为宗旨,开展了基于规则大数据分析的质量管控技术研究。研究复杂产品质量管控技术在航空制造业的应用情况,分析并梳理成飞公司质量管理的现状。以“精准定位”、“反哺生产”为管控目标,构建基于大数据分析的质量管控体系。研究基于MaHout数据挖掘技术的应用模式,实现流程依据挖掘出的关键信息自动控制质量管理的集成应用。基于飞机产品制造过程质量检验与控制业务,研究基于统计过程控制方案及稳定性预警技术,实现产品制造过程质量管控模式从事后被动检验转变为事前主动预防,从而达到提高产品质量及成品率。建立质量管控平台,开发完成生产计划执行情况数据分析、物料配套数据分析、现场执行数据分析、检验数据分析,与PDM/CAPP/ERP等系统的集成,实现生产质量的全过程管控。梳理零件、装配生产制造的质量控制业务流程,建立业务流程对应的质量指标数据,实现业务流程与指标数据采集的协同管控。研究单机质量交付状态清理的业务流程和大数据分析相关技术,实现单机质量交付状态的快速清理。建立QBOM的目录体系结构,通过数据分类和整理,实现QBOM目录结构的单机质量档案管理。
2.1 总体架构
基于大数据的质量管控总体技术架构如图2所示,整体分为大数据技术集成环境、大数据应用开发工具和大数据业务应用三个部分。
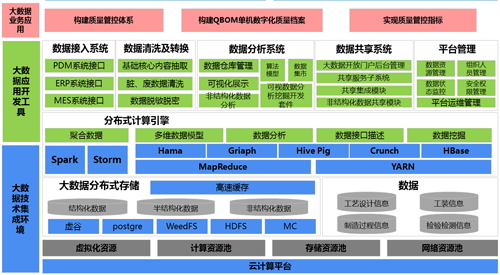
图2 系统架构图
大数据技术集成环境是进行大数据分析的技术和平台基础。搭建基于云计算和HDFS的虚拟化资源池、存储资源池、网络资源池以及基于Spark的计算资源池,形成能够处理各类数据的大数据分析环境,主要处理的数据包括结构化数据、非结构化数据及半结构化数据等按数据结构划分的数据和工艺设计数据、工装数据、制造过程数据、检验数据等按业务划分的数据。大数据应用开发平台工具是进行质量管控的中间层,主要包含分布式计算引擎、业务数据接入系统、数据清洗转换过程、数据分析系统和数据共享系统。大数据业务应用层是质量管控的业务分析层,主要包括构建质量管控体系、构建QBOM单机数字化质量档案、实现质量管控指标等内容。
2.2 主要内容
基于大数据的飞机质量管控的复杂性首先体现在实物相关的质量信息数据分类多、数据信息大、质量数据流程复杂等特点,本次技术研究主要以业务流程为导向,建立了质量信息采集控制管理流程,从开始零件原材料下料到零件投产,后续制造质量数据采集、到零件交付归档,以及在实际制造过程中的实测记录值等,都有严格的流程控制,系統梳理了每一个控制流程节点应该采集的数据值信息,规范了质量数据信息采集的流程和数据的规范性,建立了飞机制造过程质量管理体系。
从装配环节来说,同样梳理相应的质量管理流程和数据采集数据信息,同时装配主要质量很大程度上也取决于配套零件、成品、标件等子件信息数据,系统通过配套管理和二次配套管理有效解决装机信息管理问题,同时与质量单据信息系统集成,包括质量单据系统与设计集成,实现厂所协同管控的质量管控体系,不仅实现了实际AO质量 信息管理,同时AO对应装机子件的质量信息一起通过大数据技术建立实时分析关联,从而实现AO质量体系建立。
建立以QBOM为目标的单机质量档案。基于大数据的飞机质量管控的主要目标是实现以QBOM为目标的单架次产品质量档案的输出管理,系统从FO归档、AO归档、交付状态清理三个环节分别建立零件FO档案、装配AO档案、单架次产品质量信息档案。FO归档实现了零件生产制造过程所有质量信息的无纸化的归档。AO 归档实现了装配生产制造过程所有质量信息的无纸化的归档。单机质量档案主要通过系统设计的合格证管理、条码技术使用、加上应用系统图号、质量编号、件号等信息,建立了零件与装配的松耦合的关系,同时通过系统设计和相关技术的使用,系统通过对合有效管理,有效解决装配环节对合对单机质量的影响,从而实现了生产管理与质量管理的协同,最终实现以QBOM为目标的单架次产品质量档案归档管理。
在国内首创了跨厂所异地协同RFV(不一致处理单)全过程数字化、流程化处理机制,解决了制造过程中不一致处置和装配执行集成管控的应用难题,实现了跨平台异地产品装配制造执行过程质量信息和过程的闭环管理。基于三维数模工艺指令构建了集生产执行管控、工艺变更控制、物流配送、质量追溯于一体的管控模型,基于QBOM建立了单机数字化质量档案,实现了装配制造现场无纸化和三维可视化。
2.3 关键技术
(1)基于分类算法的工艺改进管理
本项目通过对保留原因分类和故障原因关联分析,找出了影响工艺设计的关键因素,通过改进措施,降低了此因素的发生概率,从而提高了工艺设计成功率。
(2)实现多样化数据采集及分析,将分散数据集中管理,建立企业级质量数据库
通过本项目将ERP、PDM、RFV等多个生产系统中质量相关的结构化数据,以及这些系统的日志文件,图形文件等非结构化数据进行统一采集和管理,建立了企业级质量数据库。
(3) 高效的数据分析功能
本项目通过使用Spark数据分析工具,能够快速的找出影响某一指标的关键因素,实现高效分析。
(4)基于统计过程控制(SPC)的质量管控技术
结合飞机产品制造过程质量管控业务实际,对基于统计过程控制(SPC)及稳定性预警的质量管控技术进行研究,为制造过程关键工序提供质量过程统计、分析、预警、诊断全面过程管理的决策方案,及时发现关键工序生产过程的变异,消除异常波动,使生产制造处于稳定状态。
统计过程控制即应用统计学相关理论及技术对过程中的各个阶段应用控制图进行监控,对异常的点进行诊断分析,从而达到保证和改进质量的目的。本次研究基于统计过程控制的质量管控方案主要包括以下内容:
• 质量信息管理
实现生产过程关键工序的质量信息管理,提供及时的、基于分析的报告和警示,满足管理生产、审计和工业标准化质量报告的要求。
• 统计过程控制与分析
实现生产过程关键工序的过程管理、持续过程改进、提供详尽全面的一元及多元小批量的SPC分析,并对过程异常进行报警。统计过程控制(SPC)技术使用统计控制图对过程绩效及其波动因素进行监控和分析。通过建立统计控制图,可以实时地对生产过程的各种输出特性进行统计监控与分析,以便及时发现导致质量特性发生变化的异常原因,并及时剔除或减少异常原因,使质量特性的波动处于统计稳定状态。统计过程控制及分析模块基于质量特性的相关性分析、过程能力分析等关键技术,提供用于常规过程管理、持续过程改进、针对不同特点和类型的SPC控制图(包括一元常规控制图、小批量计量值控制图、多元计量值控制图),并提供报警系统(通过判断控制限、警示限及违反模式进行监控过程的报警)。
• 统计过程诊断
通过对工序质量影响因素的分析,实现对过程异常发生原因和地点的诊断,为迅速解决质量问题提供方向和目标。统计过程诊断(SPD)模块根据质量指标的一元及多元性,分别采用不同的方法,对异常工序或对多质量指标中的异常质量指标进行定位,从而帮助操作人员及时识别、判断、分析和处理异常,并对生产进行改进。该模块基于主成分分析法(PCA)来实现多元SPD的诊断,其基本思路如下:寻找一组新变量(即主成分)来代替原变量,当SPC控制图出现异常点,就需要通过制作各主成分的单变量控制图,将各质量特性的对失控主成分的贡献率进行比较分析,从而实现工序异常判断。
4 结束语
本文研究了基于大数据的飞机质量管控关键技术,将现代信息技术、自动化技术、先进制造技术、现代测量技术相结合,综合应用于飞机的产品设计、工艺设计、生产制造及检验检测等生命周期管理的各个阶段[3]。应用大数据平台集成各个业务系统质量数据,通过产品模型的质量控制、质量数据的自动采集、分析与反馈控制以及质量信息资源的共享和质量管理的协同,建立一套以数字化、集成化、网络化、协同化为特征,预警和报警相结合的飞机制造质量管控框架系统。本技术应用于飞机生产过程,取得了良好的经济效益和社会效益。
参考文献:
[1] 蒲娟,许建新,王凯,王成,飞机制造质量保证技术研究[J],机械制造,2014.
[2] 余志强,陈嵩,孙炜,基于MBD的三维数模在飞机制造过程中的应用[J].航空制造技术,2009(S2).
[3] 张根保,任显林,李明,等.基于MES和CAPP的动态质量可追溯系统[J].计算机集成制造系统,2010(2).